Producing a Welding WPS: Step-by-Step Recommendations for Professionals
Producing a Welding WPS: Step-by-Step Recommendations for Professionals
Blog Article
The Ultimate Guide to Welding WPS Procedures: An Extensive Review for Welders
In the elaborate world of welding, Welding Treatment Specs (WPS) function as the backbone of guaranteeing top quality, uniformity, and safety in welding operations. Recognizing the nuances of producing, implementing, and monitoring WPS procedures is vital for welders looking to raise their craft and satisfy market requirements. As we dig right into the numerous elements of a WPS and check out the complexities of certification and certification, we will reveal the important role these treatments play in the world of welding. Allow's begin on a journey to decipher the complexities and significance of WPS procedures in welding practices.
Importance of WPS Procedures
Comprehending the importance of Welding Procedure Specifications (WPS) treatments is important for guaranteeing the top quality and honesty of welded structures. WPS procedures work as a roadmap for welders, detailing the essential steps, parameters, and products required to attain a sound weld. By sticking to WPS guidelines, welders can make sure consistency in their job, bring about structurally sound and reliable welds.
Among the primary reasons that WPS procedures are essential is their duty in preserving weld high quality and stability. Following the specified welding parameters and strategies described in the WPS helps stop flaws such as porosity, cracking, or insufficient combination, which can compromise the toughness and longevity of the weld. In addition, WPS procedures are crucial for making sure conformity with industry requirements and codes. By adhering to recognized WPS guidelines, welders can demonstrate that their work fulfills the required needs for safety and high quality, offering guarantee to customers, examiners, and regulatory bodies. Fundamentally, the significance of WPS procedures can not be overemphasized, as they are fundamental to attaining consistent, high-quality welds that meet market criteria and specifications.
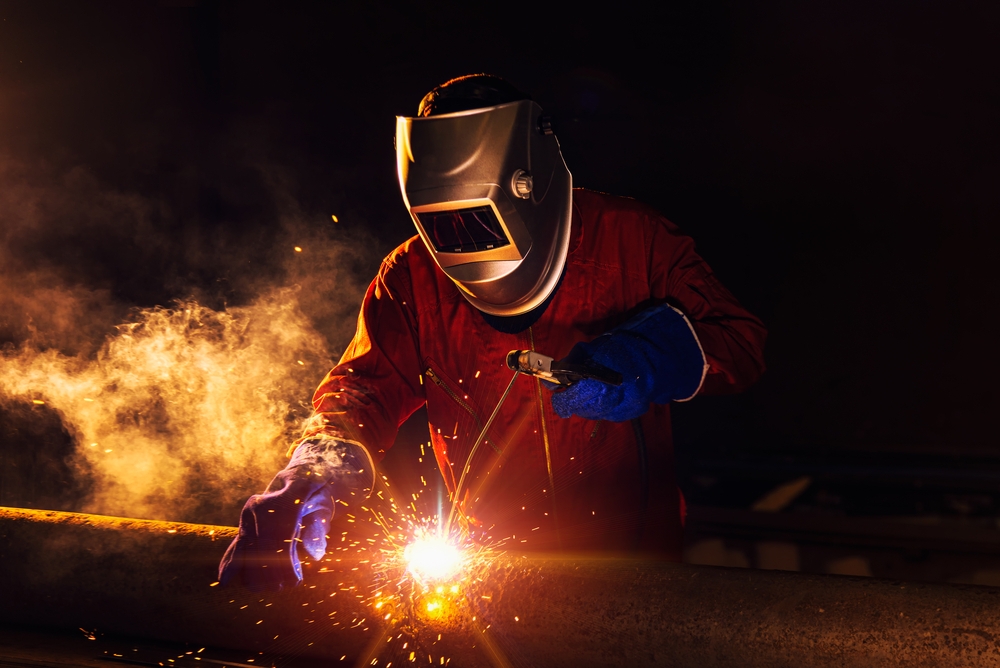
Elements of a WPS
A Welding Treatment Requirements (WPS) normally makes up important components that information the certain requirements for executing a weld, making sure uniformity and quality in the welding procedure. The crucial components of a WPS include essential variables such as base steels, filler metals, interpass and preheat temperature levels, welding procedures, protecting gases, welding settings, and post-weld heat therapy demands.
Base metals refer to the products being joined, while filler steels are used to fill the void between the base metals during welding. The welding process describes the particular method to be used, whether it's gas steel arc welding (GMAW), secured metal arc welding (SMAW), or one more technique. Welding positions specify the orientations in which welding can be carried out.

Credentials and Accreditation
Having established the essential components of a Welding Procedure Specification (WPS), the emphasis now shifts towards the important aspects of credentials and qualification in welding practices.
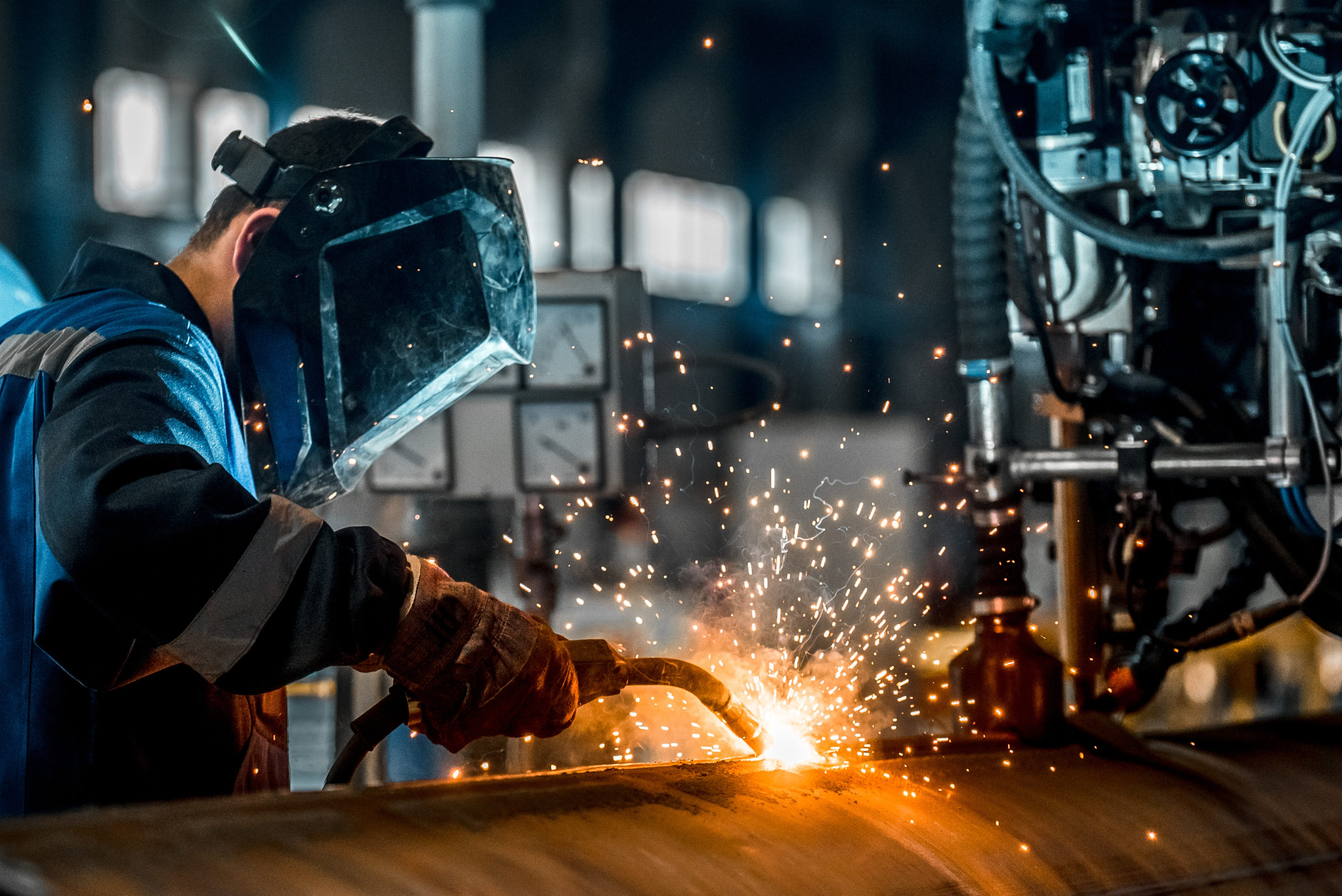
Accreditation, on the various other hand, is the formal recognition of a welder's credentials by a pertinent certification body or organization. Welding qualifications are commonly based upon the particular welding procedures, materials, and placements a welder is certified to collaborate with. Holding a valid welding qualification shows that a welder meets sector standards and is competent to execute welding tasks to the required specs.
Developing a WPS
To create a Welding Treatment Specification (WPS) that satisfies sector standards, mindful consideration of welding processes, materials, and operational parameters is vital (welding WPS). The primary step in developing a WPS is to identify the welding process to be used, such as gas metal arc welding (GMAW) or secured steel arc welding (SMAW) As soon as the welding procedure is determined, the next essential facet is selecting the suitable products, thinking about aspects like base steel kind, density, and joint design. Functional criteria such as welding present, voltage, travel rate, and shielding gas composition need to additionally be carefully defined in the WPS.
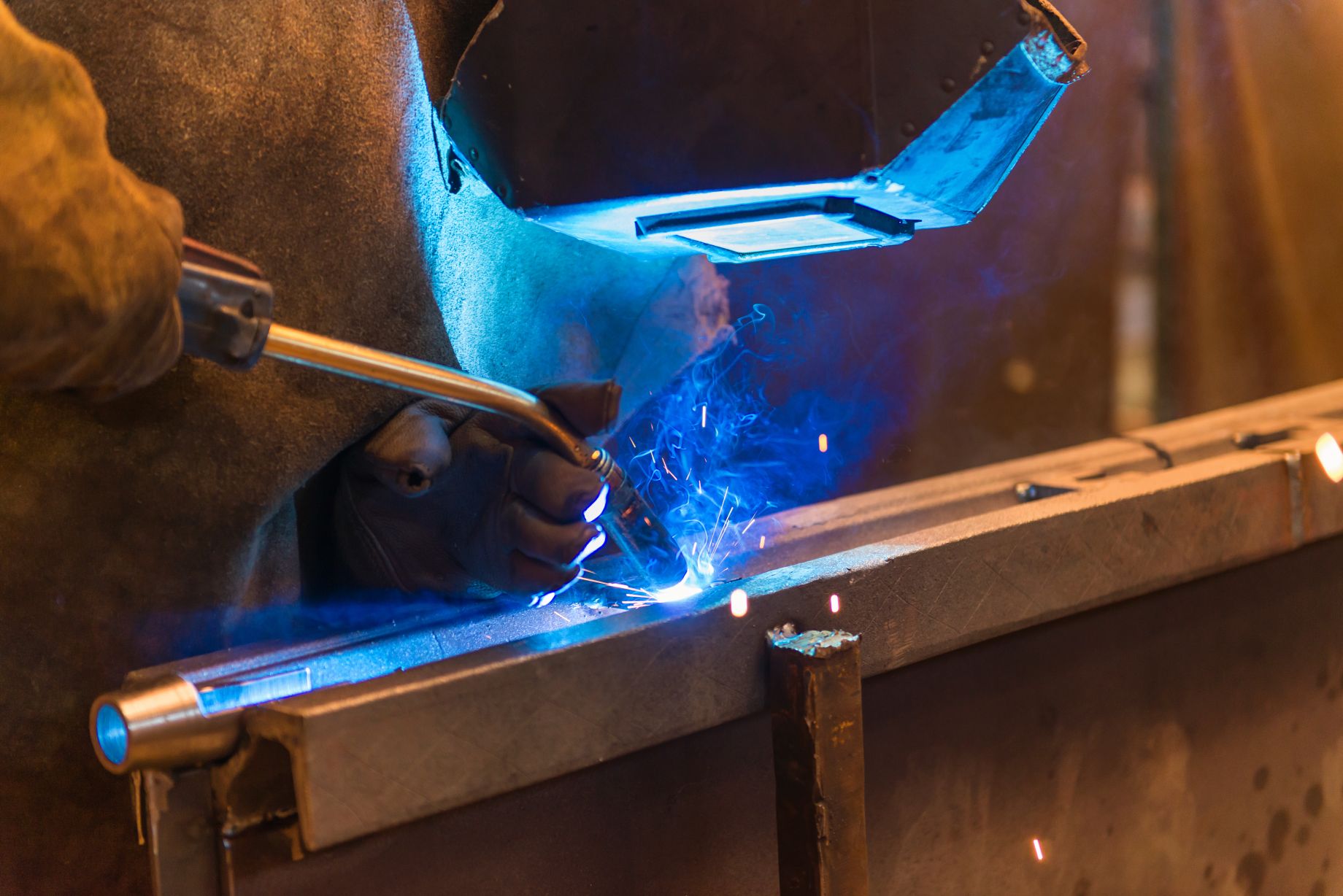
Executing and Keeping Track Of WPS
Upon wrapping up the detailed Welding Treatment Spec (WPS) that diligently details welding processes, products, functional criteria, and top quality assurance procedures, the emphasis changes to properly applying and monitoring the established treatments. Execution includes making certain that all welders entailed in the project are familiar with the WPS and follow it meticulously throughout the welding procedure. Reliable execution and surveillance of the WPS are important for guaranteeing the honesty, stamina, and safety of the welded joints, eventually adding to the general success of the welding job.
Final Thought
In verdict, understanding and complying with Welding try here Procedure Requirements (WPS) is vital for welders to make sure high quality, consistency, and safety in their work. By recognizing the parts of a WPS, obtaining correct credentials and accreditations, developing thorough treatments, and applying and checking them properly, welders can enhance their abilities and efficiency in welding methods. Complying with WPS treatments is important for look at this web-site producing top quality welds and conference industry standards.
In the detailed world of welding, Welding Procedure Requirements (WPS) serve as the foundation of ensuring high quality, consistency, and safety and security in welding procedures. The welding procedure lays out the details method to be utilized, whether it's gas metal arc welding (GMAW), secured steel arc welding (SMAW), or another technique.To establish a Welding Procedure Requirements (WPS) that meets industry standards, cautious consideration of welding processes, materials, and functional criteria is important. The first step in developing a WPS is to recognize the welding process to be utilized, such as gas metal arc welding (GMAW) or secured steel arc welding (SMAW)Upon settling the comprehensive Welding Procedure Specification (WPS) that meticulously information go to the website welding processes, materials, functional specifications, and top quality guarantee steps, the focus changes to efficiently carrying out and keeping an eye on the well established treatments.
Report this page